Flat die wood pellet production line
Application for Various Biomass Materials
Complete Flat Die Pellet Line for a Small Biomass Pellet Plant, featuring a flat die pellet mill, includes the following process:
The wood pellet complete production line comprises a crusher, hammer mill, dryer, pellet machine, cooler, and packing machine, etc.
First, biomass raw materials are crushed into powder particles via a crusher or hammer mill. The crushed materials are then dried to retain 15-20% moisture content for optimal pelleting conditions. Materials are transferred to a silo or bunker bin via a screw elevator and fed into the flat die pellet machine. Finished pellets are cooled and screened by a cooling screening machine, then packed and sealed via a belt conveyor.
Equipment configurations can be adjusted or omitted based on specific requirements. For example:
Self-use pellets may skip the counterflow cooler and packaging machine.
The dryer is optional, depending on material moisture content.
Hourly Capacity Options: 100-200kg/hr, 300-400kg/hr, 400-600kg/hr, 600-800kg/hr, or 800-1000kg/hr. The Flat Die Pellet Line is ideal for beginners due to its compact layout.
Whole Process Show
1. Crushing system
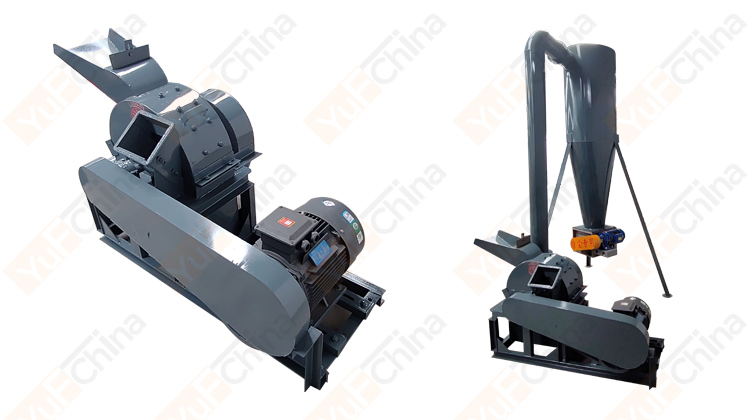
Multi-Function Hammer Mill is needed if raw materials as wood with diameter ≤20cm. Being Feed into the crushing chamer by #1 Inlet, then the crushed powder will be set out from the mesh screen by the force of centrifugal pressure and fan suction.
2. Dryer system
The humidity of sawdust will be controlled by a Airflow Dryer or a Rotary Drum Dryer.
Both the rotary drier and air-flow dryer are drying the wet materials by hot air. Hot-air Furnace (Heat Exchange Chamber) will be installed to provide heating air for the whole drying section, Fuels are optional by wood, biomass pellet, gas, fuel oil, etc.
In different cased we have the specific choice for the drying machine.
Sometimes after dryingwe collect dried materials with moisture between 8% and 20%.
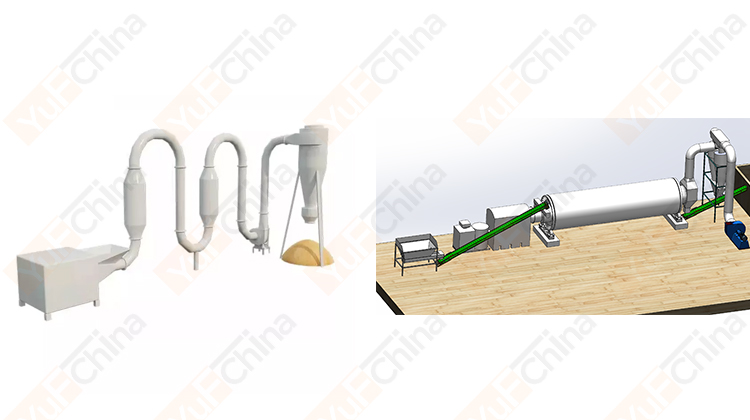
3. Pellet system
By auger feeder, the Farm Waste Pellets Machine is composed of a bunker, press roller, flat die, reducer and motor, which is used to produce dense fuel pellet from biomass raw materials through the extrusion of the press roller and the flat die.
Die Specification plays important role for the smoothly production, on the basis of qualified type and humidility of raw materials, we should take more attention for the Die Compress Ratio.
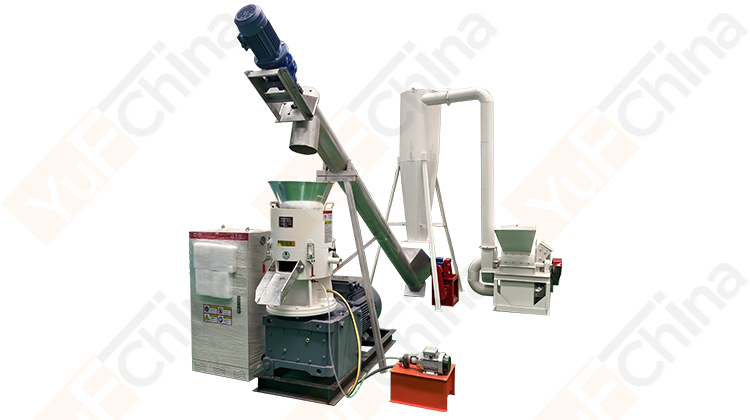
4. Cooling and Screening system
Simple Structure Pellet cooller & screen machine is designed speciall for the small scale pellet plant factory.
Considering the cost, YuFChina also design a new type of Chain Coolling Conveyor to finish the 3 in 1 Functions, which are used for pellet coolling, screening and transporting. With long Long life, simple maintenance,simple operation and so on.
We will recommed the suitable ones according to your budget, site conditions and production capacity.
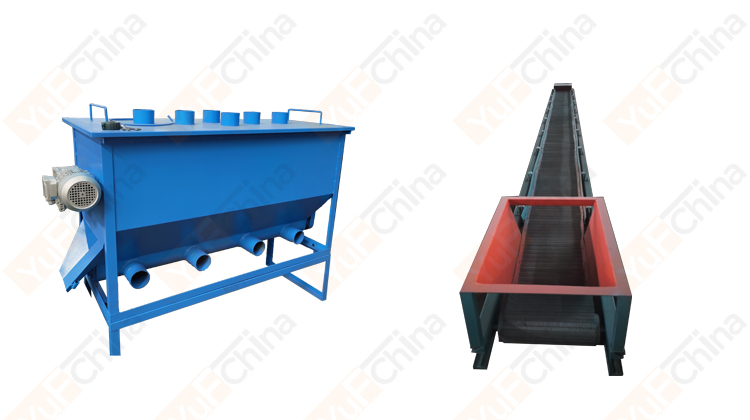
5.Packing system
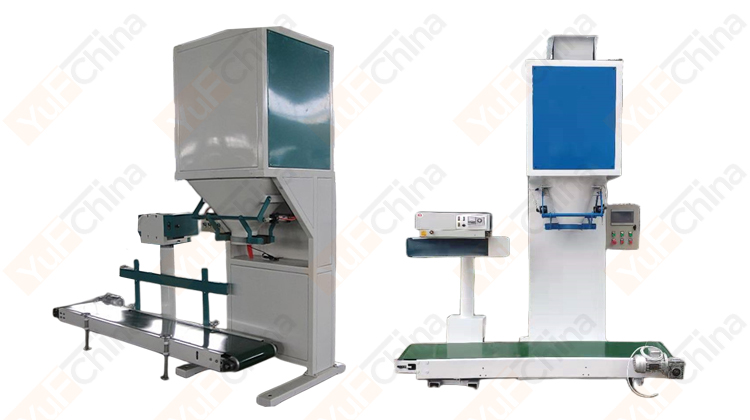
by Weight, Sealing, Transporting, the Packing machine used for quantitative packaging of granular materials in feed, grain, fertilizer, rice, seed, chemical, food and other industries.
Advantage: Automatic Control, Adjustable Feeding Speed, Precision and easy to operate.
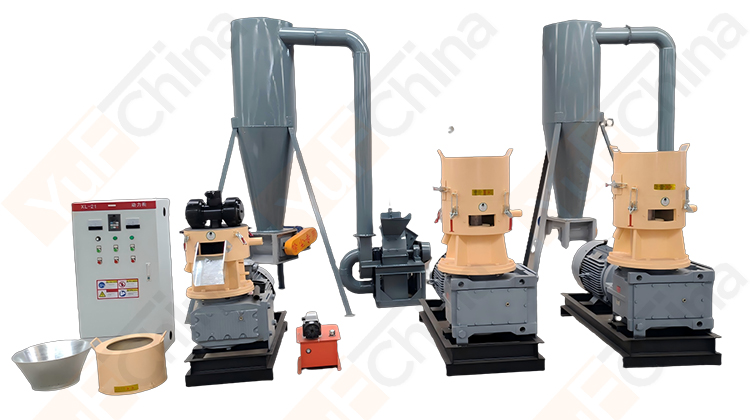
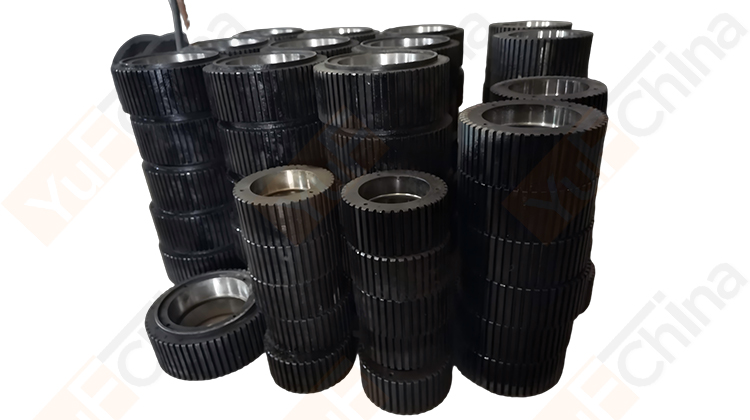
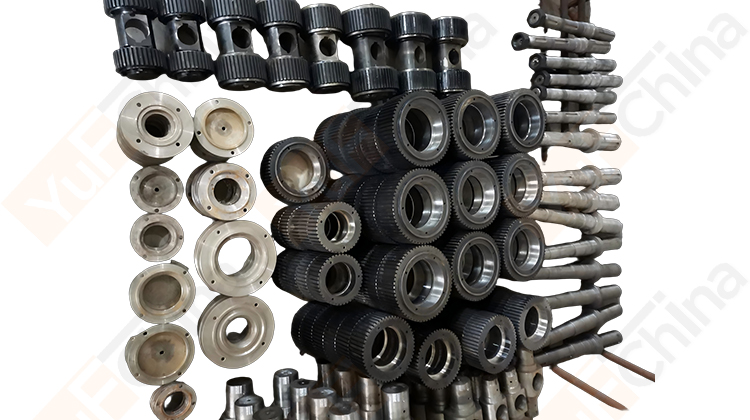
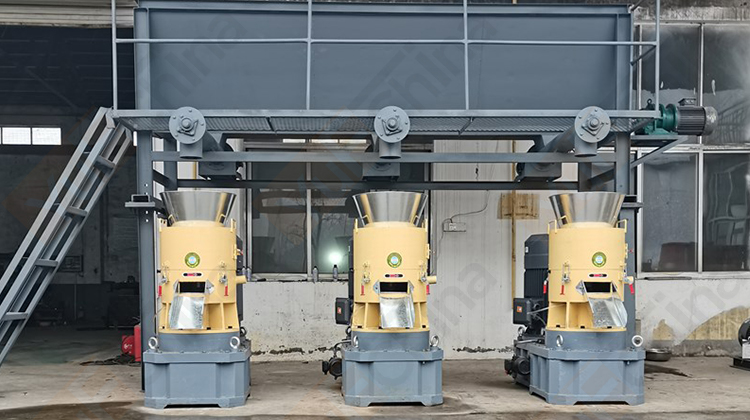
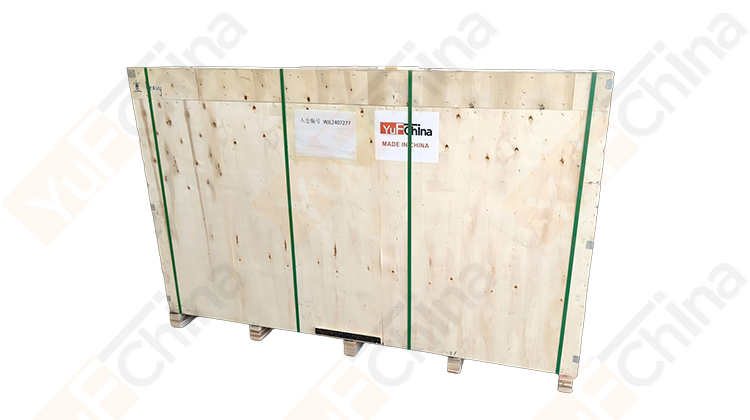
The specific components of the wood pellet plant can be customized to meet your requirements. For example, if you are producing pellets for self-use, you can delete the counterflow cooler and pellet packing machine. Additionally, the dryer is optional, depending on the moisture content of your materials.
Choose our complete wood pellet plant for efficient and convenient biomass pellet production tailored to your needs.
Flat Die Biomass Pellet Machine Technical Data
Model | Power (kw) | Capacity for wood (kg/hr) |
---|---|---|
200 | 7.5 | 80-100 |
260 | 15 | 100-200 |
300 | 22 | 200-300 |
350 | 30 | 300-400 |
400 | 37 | 400-500 |
450 | 45 | 500-600 |
450 | 55 | 600-800 |
560 | 75 | 800-1000 |
GET IN TOUCH WITH US