How Important of De-ironing in biomass pellet production?
Today, I am going to show you the actual cases in our clients’ site, and explain why we particularly emphasize the importance of adopting the iron removal device in the pelletizing process. Please take a look at the following pictures first:
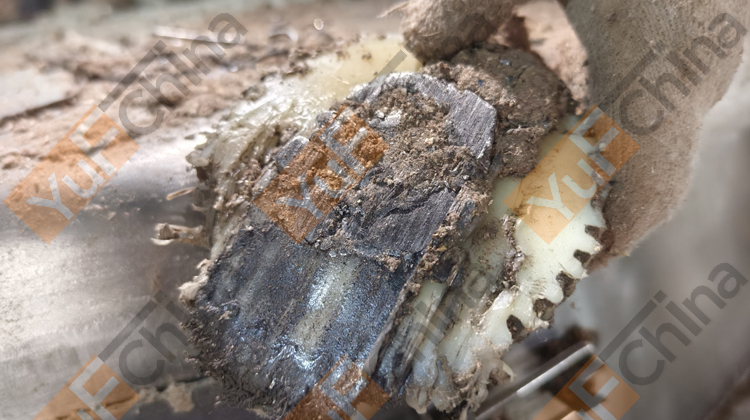
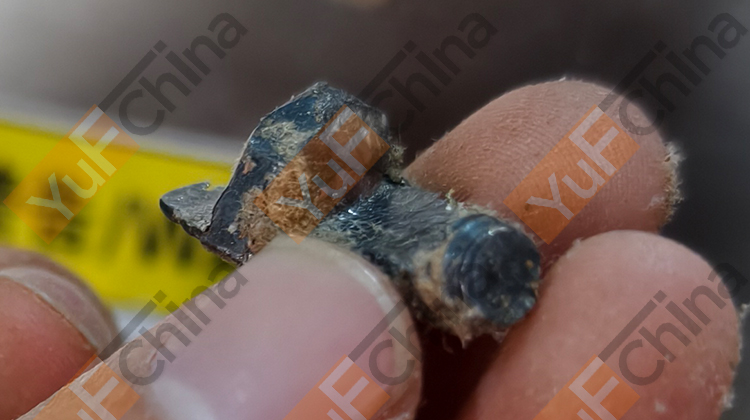
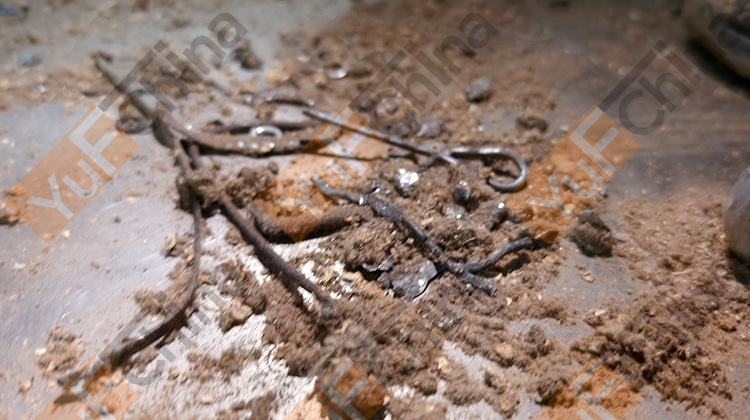
During a test run, our sales technical found an abnormal sound in the pelletizing chamber, so he quickly stopped the pellet mill and opened the pelletizing chamber for inspection. There were a variety of impurities in the pelletizing chamber, including nails, nuts, bearing steel balls, bearings, rope ends and cloth ends, etc. These metal products are the biggest threat to the smoothly operation of the pellet machine, which may cause shutdowns and stop the production. It may fast Wear the holes of ring die, reduce the production and more seriously, they may damage the ring die and roller assembly. The roller skin also be damaged frequently by the extrusion of foreign objects, and related parts need to be replaced often. This not only causes direct economic losses, but may also bring greater indirect losses.
The iron impurities above were founded in only two hours of testing.
Next, let's look at the raw materials used by the customer:
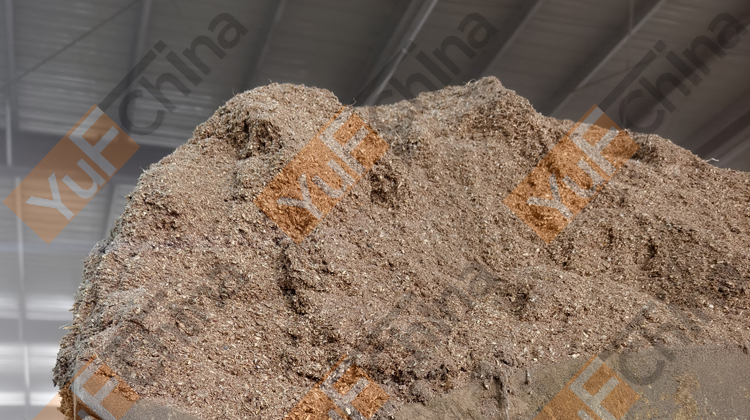
The raw material is mainly composed of corn cob slag and waste from cotton spinning mills. It is difficult to determine whether there are iron items (such as nuts, nails, wires, etc.) inside. However, in the actual process, these hidden iron impurities frequently appear, threatening the service life of the ring die and the pressure roller, and causing a significant impact on ordinary production capacity.
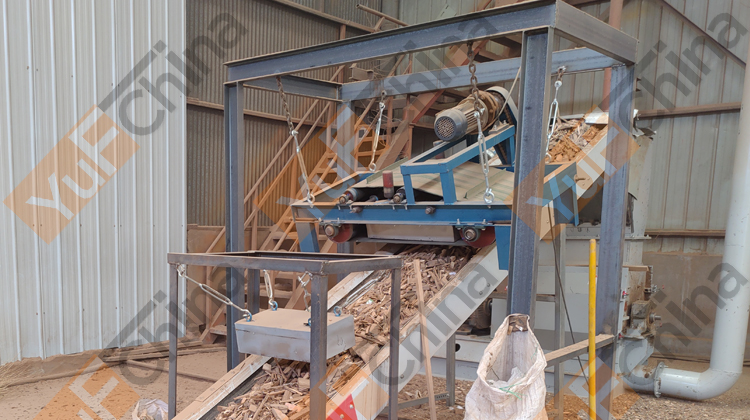
In order to remove the iron impurities, we usually recommend the automatic iron removers or static type of strong magnetic blocks. Automatic iron removers should be installed at the feeding belt conveyor to ensure that iron debris can be separated before the material enters the hammer mill and pellet mills. Refer to the auger feeder, we recommend that strong magnetic blocks be placed both at the feed & discharge port to achieve the best iron removal effect, ensure the smoothness of the subsequent processing process and extend the life of the equipment.
To sum up, although the installation of an iron remover will increase the initial investment, it can bring higher production safety in the long run, with better product quality and lower maintenance costs, thereby bringing greater economic benefits and market competitiveness to the enterprise.
GET IN TOUCH WITH US