Some Reasons For Roller Bearing Burnt Out
When you running the biomass pellet plant, the healthy operation of the rollers is directly related to your production and pellet quality. However, damage of roller bearing is a common problem that blocked your production or even cause more serious equipment damage. In order to ensure the continuously production and stable equipment running, it is crucial to understand the reasons of bearing damage and take preventive measures. This article will remind several possible that causes of roller bearing damage and how to prevent the bearing damage.
1. check lubricant pipe if being blocked (lack of lubricant)
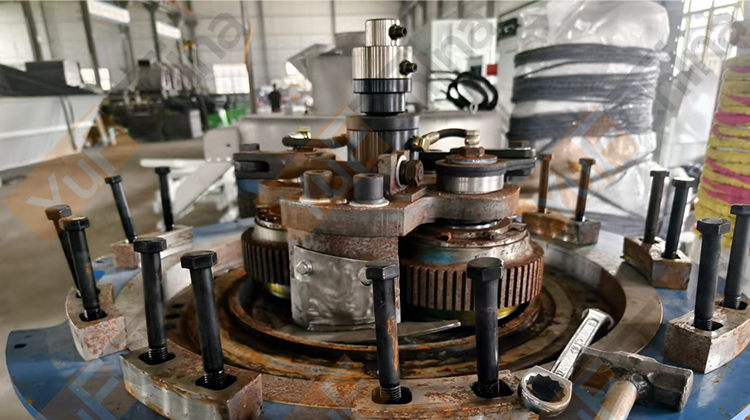
The most common reason that causes of bearing damage is blocked oil circuits or insufficient lubrication. When the bearing lacks sufficient lubrication, friction increases, and resulting in accelerated wear. Therefore, it is critical to check the adequacy of the roller lubricant before starting the pellet mill. For a newly installed pellet mill and the one which you just replaced the roller skin, it is necessary to start the automatic lubricant pump before you run with loading. (usually it takes about 30-40 minutes). You can observe whether there is lubrication coming out of the press cover to ensure the smoothly lubrication pipes, otherwise it may cause dry bearing burnt and damage.
2. wrong compress ratio, which makes pellet too dark and hard, machine shell high temperature and ammeter unstable.
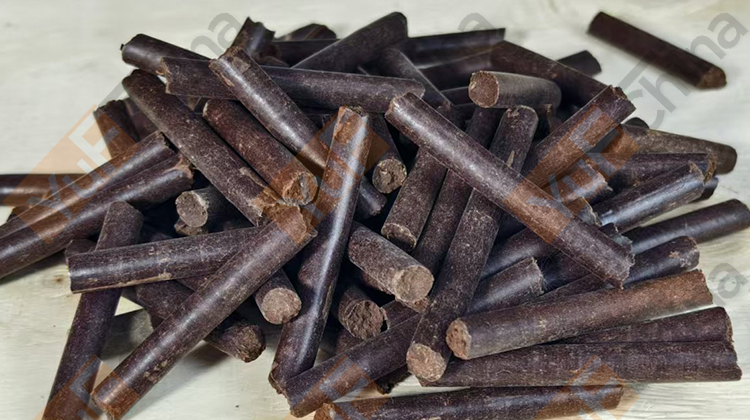
When you change the type and source of raw materials, exist compress ratio of ring die may no longer be suitable for the new materials. When the following situations occur, you should replace it with the the appropriate ring die on time to prevent the bearing damage.
Pellet more harder and color becomes dark.
Temperature of pellet mill shell becomes higher
The ammeter becomes unstable
3. check raw materials moisture (too much steam, machine shell high temperature, ammeter unstable)
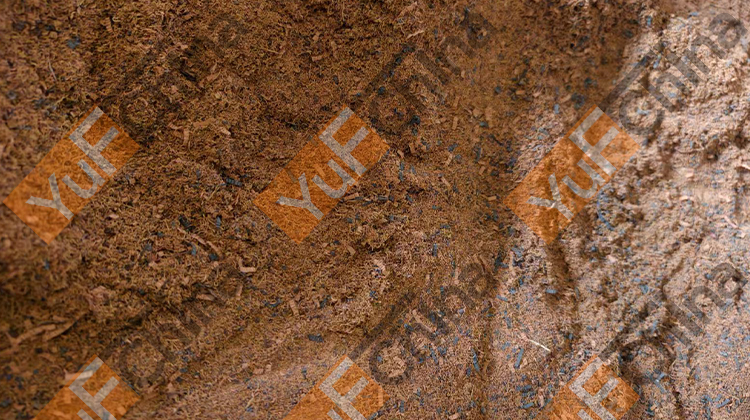
High humidity of raw materials will also cause problem for the bearing. High humidity of raw materials will give more pressure for the roller and pellet mill. Then you will find the temperature of pellet mill shell becomes higher, and ammeter becomes unstable. All those condition will cause bearing damage.
4. check lubricant quality (less drop temperature)
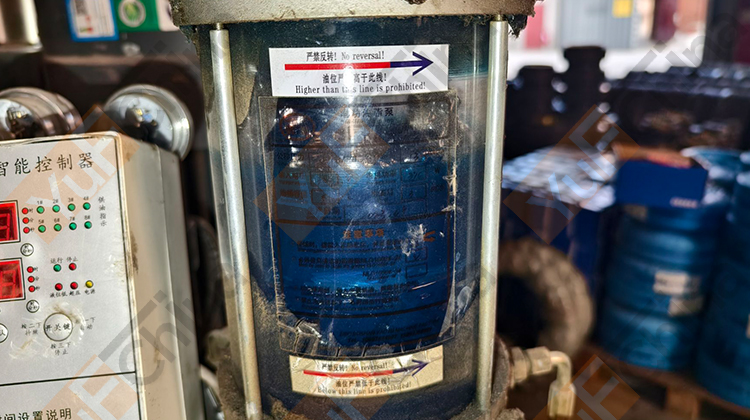
The quality of grease is also an important factor affecting the service period of bearings. The dropping point refers to the temperature at which lubricating grease begins to drip at a certain temperature. If the dropping point of lubricating grease is too low, it may lose its lubricating effect in a high temperature environment, exposing the bearing to a greater risk of wear. Therefore, when using lubricating grease, it is necessary to ensure that its quality is qualified and can provide sufficient lubrication at the expected operating temperature.
In summary, to prevent roller bearing damage, we should take points as follows, clean the roller's running environment, material quality, smooth oil circuit grease quality, etc. Regular maintenance, reasonable lubrication, and qualified lubricants are the key to maintaining bearing performance and extending its service life. At the same time, any abnormal situation should be diagnosed and handled in a timely manner to prevent production risks and economic losses caused by bearing damage.
GET IN TOUCH WITH US